- TOP
- Research and Development
- Fundamental and Elemental Technologies
Materials Development
Our research and development (R&D) efforts are focused on responding to diverse demands for aluminum alloys, such as high strength, corrosion resistance, and improved formability, by developing alloys and manufacturing processes that use our wide-ranging evaluation equipment. We are also committed to developing innovative products that meet the demands of new market opportunities.
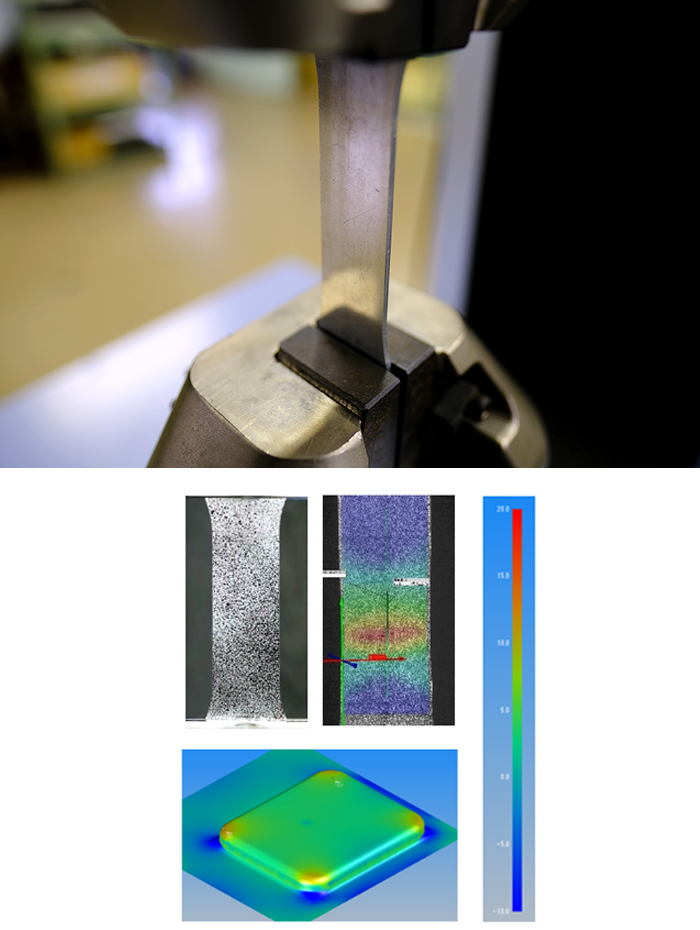
Forming Technologies
In addition to basic formability evaluation technologies, MA Aluminum has developed and proposed a variety of formability evaluation methods to meet the needs of our customers’ specific forming applications. We are also tackling the development of new high-formability products through an enhanced understanding of forming mechanisms and clarifying forming defect mechanisms via finite element (FE) simulations. Using these technologies, we are creating forming applications for sheet, foil, and extrusion products that support customer product and technology developments. We are also developing whole new process technologies that will contribute to future society.
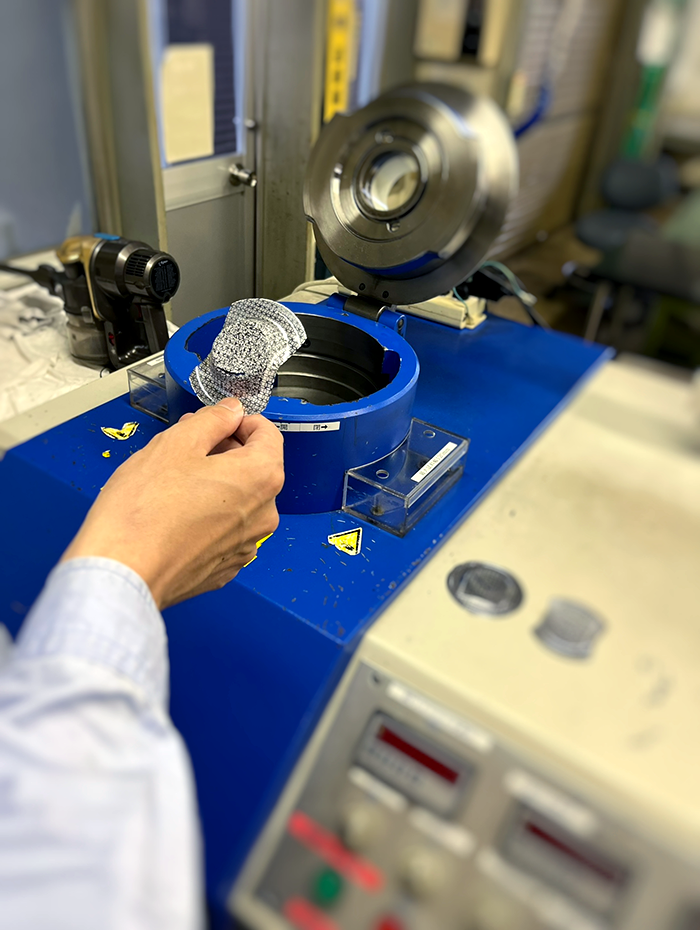
Corrosion Protection and Brazing Technologies
The materials used in heat exchangers require various properties such as formability, strength, brazability, and corrosion resistance. To facilitate the design of such products, cladding materials (brazing sheets) with filler materials filler materials and/ or sacrifices incorporated into their core material surfaces are used to improve brazability and corrosion resistance characteristics.
- We have been developing superior aluminum alloy and cladding materials with excellent brazability by selecting optimal alloy elements and cladding ratios and by controlling the structures of the core materials used.
- Cathodic protection elements (such as sacrificial anode fins, etc.) are used to provide heat exchangers with good corrosion resistance.
- We have created sacrificial anode fins and cladding materials with superior corrosion resistance; these were developed while considering element diffusion behavior during brazing.
- ・ We perform the potential prediction, protection design, and shape prediction needed for part joining processes by utilizing simulation technologies and multiple regression analysis.

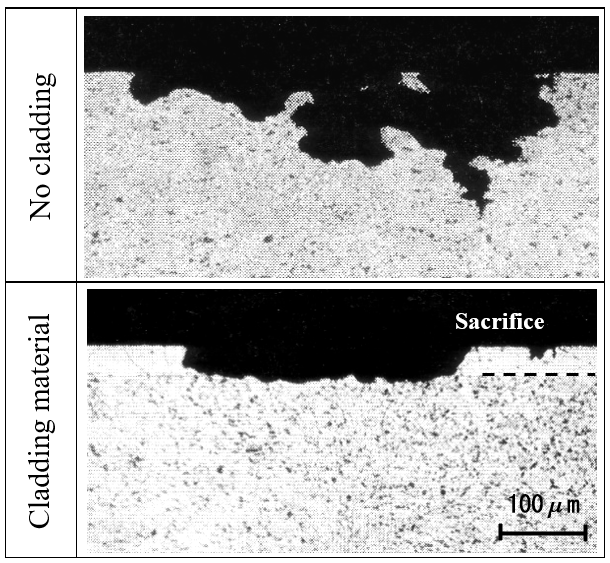
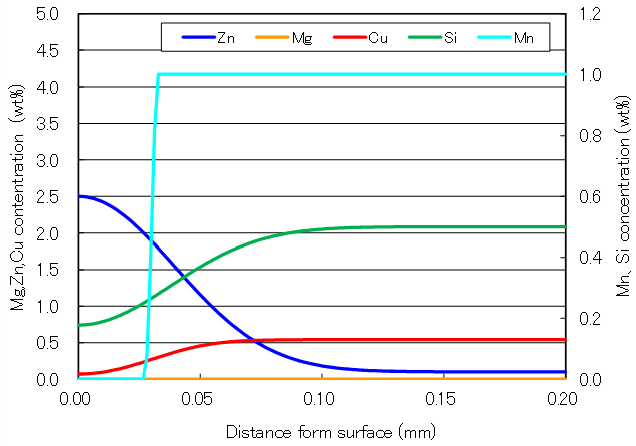
Structural Design Technologies
MA Aluminum's structural design technology supports a wide range of requests not only for materials but also for parts and subassemblies. For example, in the case of energy absorbing members, if you provide design requirements including load characteristics, we can provide customized designs that are well-balanced in terms of weight, performance, and cost through the simulation technologies that we have cultivated over many years and which are based on specialized knowledge in areas such as material selection, cross-sectional design, processing, joining methods and productivity. We also carry out prototyping and evaluation in-house and work continuously to improve our design technology based on result feedback.
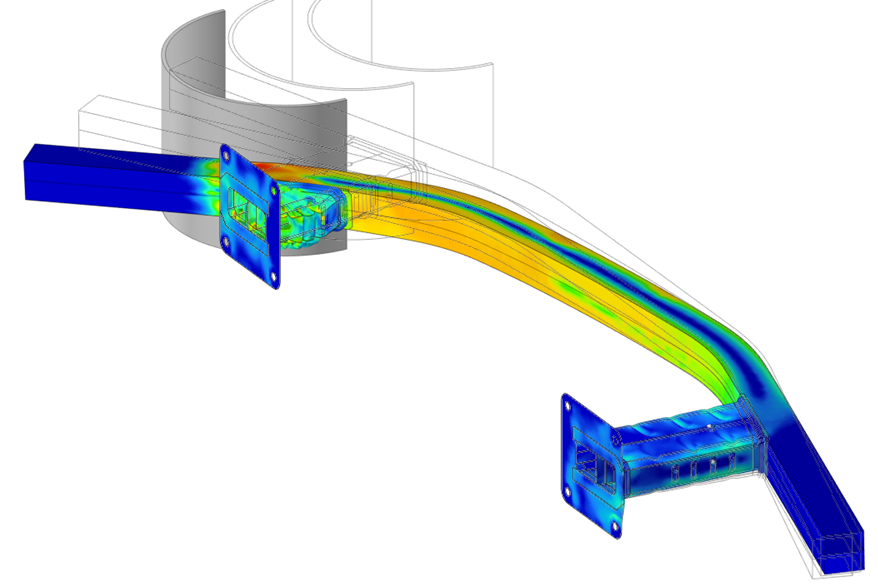
Battery Fabrication and Evaluation
We have the fabrication facilities necessary to experimentally produce and evaluate lithium-ion batteries (LIBs). In addition to assessment investigations ranging from electrode fabrication to cell assembly and charge-discharge characteristic assessments, we can also perform electrochemical measurements such as cyclic voltammetry (CV) and linear sweep voltammetry (LSV). By manufacturing LIBs and evaluating their characteristics ourselves, we can develop aluminum foils for LIBs that are tailored to customer requirements.
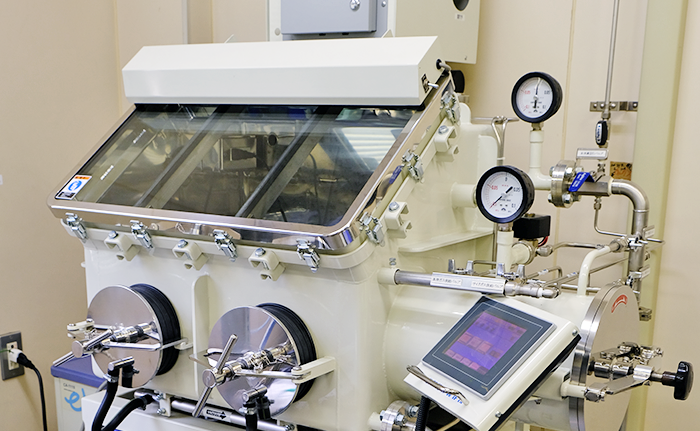
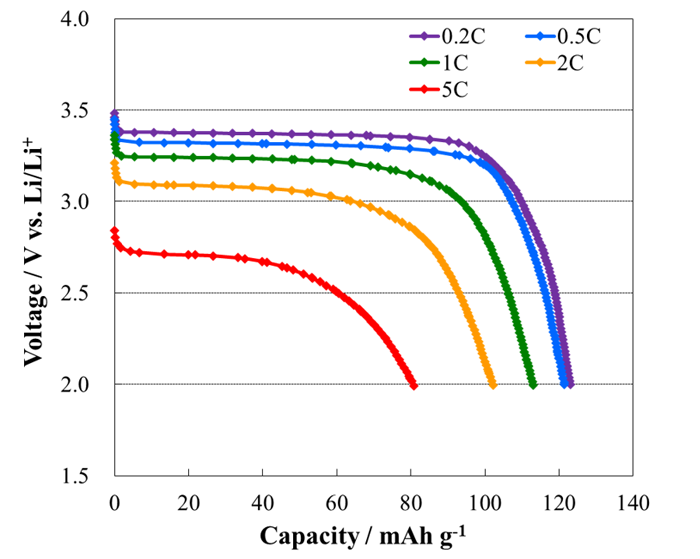
Heat Exchanger Support Technologies
MA Aluminum develops and proposes material design and manufacturing technologies that improve the performance of heat exchangers using the advantages provided by aluminum’s unique characteristics. For example, we are developing aluminum alloys that take into consideration the strength, formability, brazability, and corrosion resistance required for heat exchanger materials. In addition, we are working to meet customer requests and provide technical support by pressure resistance simulations to evaluate the heat exchange performance of heat transfer tubes and to design optimal cross-sectional shapes. Utilizing the heat exchanger material and evaluation know-how that we have accumulated over many years, we propose solutions for new issues related to the use of heat exchangers in various fields that are expected to expand in the future.
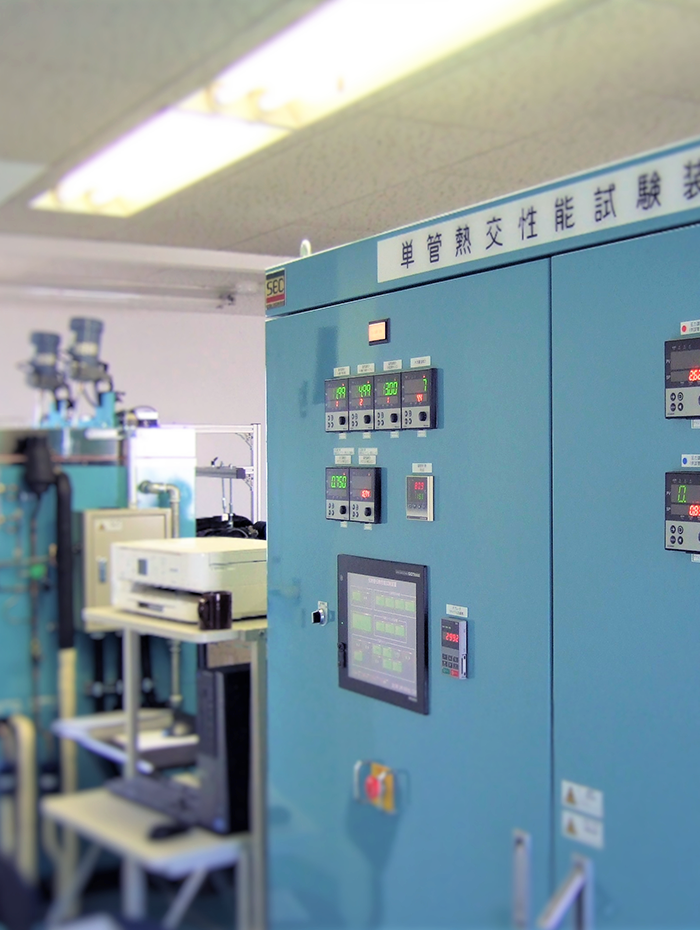
Analytical Techniques
MA Aluminum has shape observation equipment, elemental analysis equipment, chemical state analysis equipment, crystal structure analysis equipment, and micro area processing equipment for research and development purposes. Using these devices, we are accumulating the analytical technology and know-how necessary for aluminum analysis and are working on clarifying the mechanisms and phenomena of failures and defects to facilitate analyses for improving production technology. Furthermore, by conducting investigations using analysis technology, we aim to link the results obtained with functionality improvements to aluminum materials and the optimization of manufacturing processes.
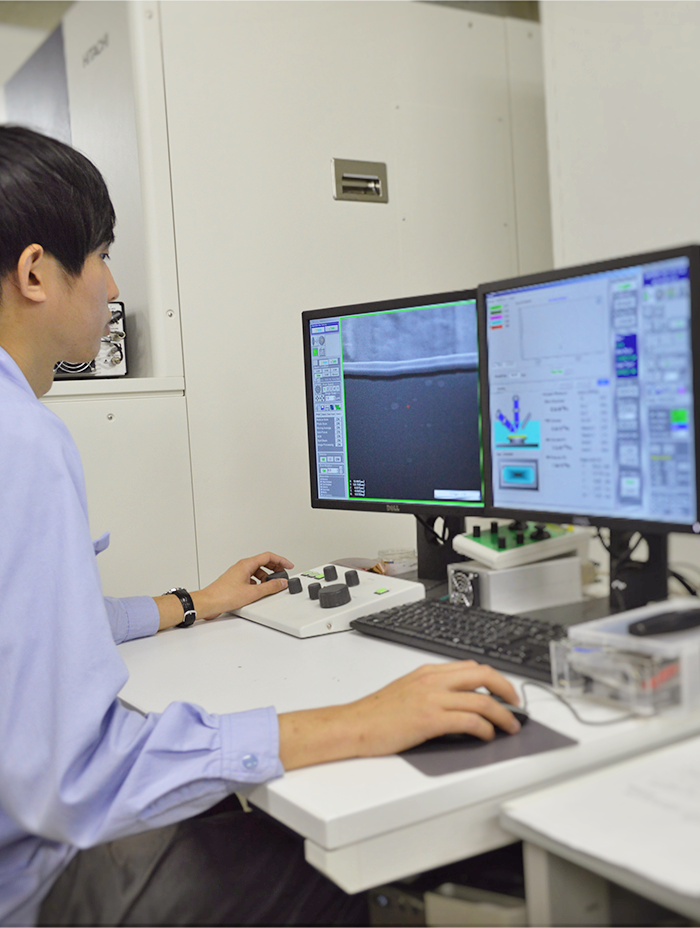
Numerical Simulations
Utilizing numerical analysis technologies, such as structural analysis, thermal fluid analysis, thermodynamic calculations, and machine learning, MA Aluminum works to improve our casting, rolling, and extrusion processes and thus achieve high quality and productivity. In addition, we use these technologies to clarify defect mechanisms during product forming and to improve product development efficiency, etc., so that we can provide better products to our customers faster.
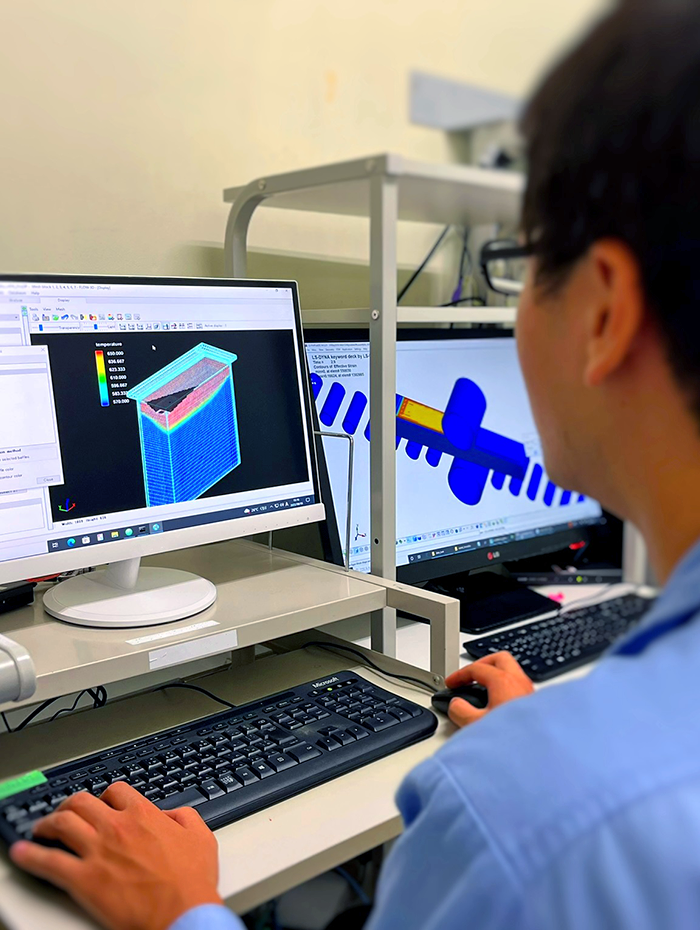